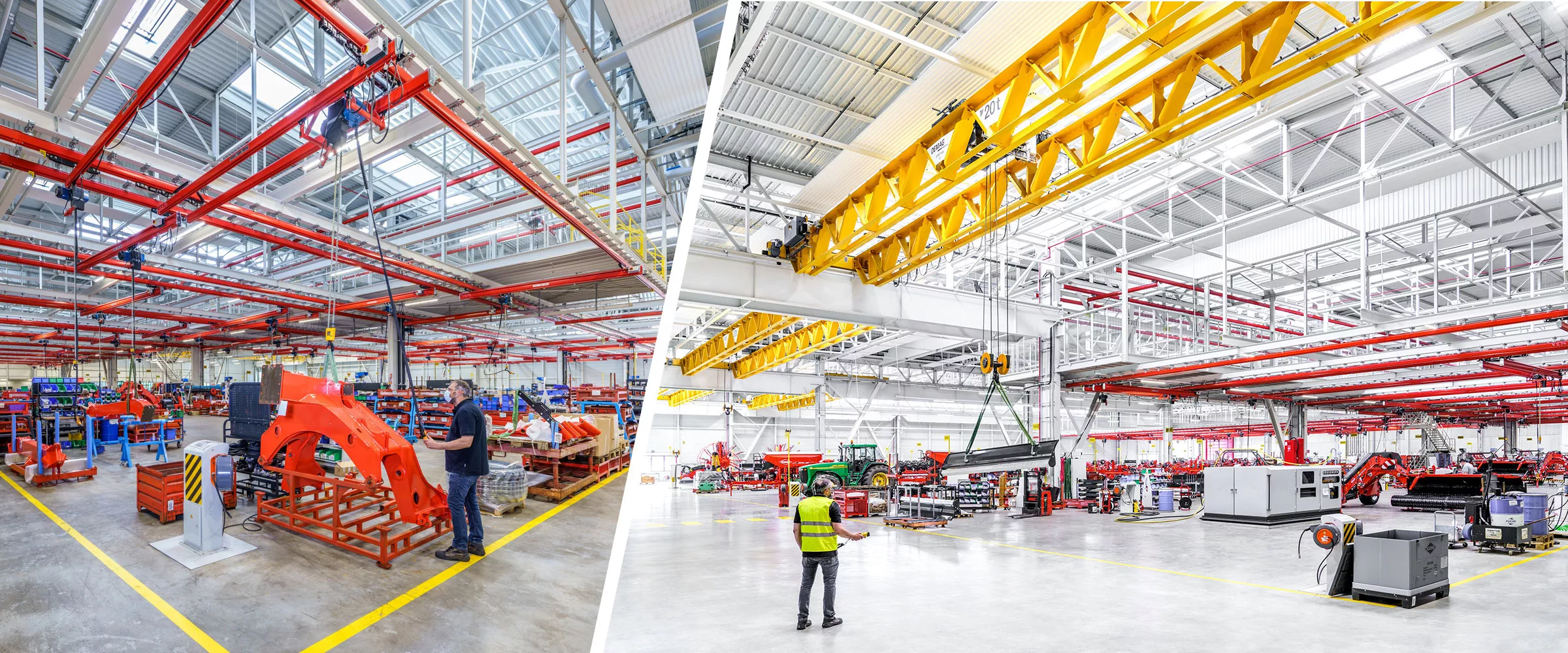
Agricultural machinery from northern France
Flexible and modular material flow
Nine V-type cranes and 3.2 km of KBK sections with 120 DC chain hoists for KUHN MGM SAS
The KUHN Group
One of the world’s leading manufacturers of agricultural machinery has its home near Strasbourg in the northeast of France. The KUHN Group promises farmers groundbreaking innovation and quality at prices in line with the market. Over 5,000 employees now work at numerous production and distribution locations in order to keep that promise all over the world.
From Alsace to the world
The company began its history with founder and namesake Joseph Kuhn as a village blacksmith shop back in 1828. Soon after, the shop specialized in making scales and measuring instruments. Then, in 1864, the company moved to Saverne and began specializing in producing agricultural machinery. Since then, its operations in the region around Saverne, including the Monswiller commune, have focused on developing, perfecting, and enhancing mowers, tedders, swathers, chaff cutters, tillage equipment, and seeders.
Requirement
Production operations at the main plant in Saverne have been expanded multiple times in the past few decades and adapted to the continuously growing demand for increasingly large agricultural machinery. However, the existing shop floor widths of only up to 15 meters limited production, making it necessary to build a new assembly plant in the neighbouring commune of Monswiller a few years ago. Related to that, the “MGM” abbreviation stands for “Montage Grande Machine” and makes it clear that shop floor widths of up to 20 meters are needed in order to assemble newer-generation agricultural machines. Accordingly, what KUHN did was build a state-of-the-art flow production facility for large agricultural machines.
Overall, the assembly plant was expanded by a total of 20,461 square meters. More specifically, 11,065 square meters for a new assembly facility, 5,437 square meters for an extension to the logistics facility, and 3,017 square meters for a shipping facility. Additional outdoor areas and a new cafeteria round out the plant premises.
Efficient production layout
The main plant in Saverne produces smaller agricultural machinery, as well as components for MGM machinery in Monswiller. The larger machinery that is used for haymaking, tilling, and sowing is assembled at the latter. These components, as well as purchased parts in the goods-in area, are picked in the “Magasin” and delivered to the assembly lines. In fact, around 100 tonnes of material are picked every month. Purchased parts and other components are powder-coated and painted at the company’s own cathodic electrodeposition shop. Assembly is carried out within the lines: The agricultural machinery is assembled step by step at the individual assembly stations, and once final assembly and functional testing are done, it is prepared for shipping.
There are delivery areas for intralogistics to the side of the assembly line. Among other things, employees need an overhead solution to transport goods brought in from the store and the paint shop to the assembly area. Moreover, material handling at the individual workstations is crucial to be able to join components precisely while making handling as smooth as possible for employees. When installing subassemblies on the main frame of an agricultural machine, lifting equipment precision in positioning and control is extremely important for efficient work. This means that light cranes are essential for every single step.
At the end of the production line, universal cranes help with final assembly. Depending on the type and size of the agricultural machinery, it is possible for bulky and heavy components to have to be installed on the main frame, making it necessary to pick them up and position them properly. The final step is functional testing, after which the finished agricultural machinery is transferred to the newly built shipping facility. Once there, cranes take care of loading the machinery onto trucks.
Solution
Expanding production operations also involved expanding the material flow strategy used for KUHN MGM: Nine ZVKE V-type girder overhead travelling cranes with an individual load capacity of 20 tonnes and 120 DC-Pro chain hoists are now assisting employees along the new assembly lines and in shipping. With a further 3.2 kilometres of KBK sections, the light crane system completely spans the new assembly lines.
KUHN MGM and Demag in France scheduled the corresponding deliveries in such a way as to ensure that the new cranes would be assembled section by section and on time. Then, after receiving appropriate training, maintenance employees assembled the light crane systems.
Modular, safe, and efficient: KBK light crane system
A dense KBK light crane system network extends along the assembly lines in Monswiller below the ceiling of the production facility. Employees move individual agricultural machinery components with KBK single-girder and double-girder cranes overhead from the logistics line to the assembly stations at the production lines, which have a length of around 100 meters and an approximate width of 25 meters. When the plant was being planned, the corresponding personnel made sure that KBK systems would be installed across the entire area to ensure that they would be available to assist with every single step.
DC-Pro chain hoists are used as the hoist units. These units have load capacities of up to 1,000 kg when moved by hand and up to 2,000 kg when moved electrically. Components can be moved smoothly with both drive methods at assembly stations, making it possible to assemble the corresponding agricultural machinery efficiently and ergonomically. Articulated connections between the crane girders and trolleys make sure that pre-assembled sub-assemblies can be smoothly handled from the assembly station to the machine frame. All throughout, the partially variable and low speeds of the DC-Pro chain hoists help crane operators easily and precisely position the above-mentioned sub-assemblies for assembly operations. Accordingly, it is just as easy to install an unwieldy roller for tilling as it is to install an electronic or hydraulic unit.
Convenience and safety when handling loads with the DC-Pro chain hoist
The compatibility of Demag components with each other ensures that KUHN MGM can even use its existing chain hoists from older generations, such as DK and even PK chain hoists. However, the employees operating the equipment have grown accustomed to the advantages behind the latest DC-Pro generation: Components can be positioned with laser precision thanks to the use of two speeds even at low speeds. With load capacities of 500 to 2,000 kg and a standard hook path of five meters, the chain hoists can be flexibly used at all workstations. The height-adjustable control cable for the DSC pendant controller, which was selected for all units, ensures optimal ergonomic comfort. And finally, the ergonomic handle shape and employees not having to switch gears when switching from one workstation to another help maximize assembly efficiency.
The DC-Pro chain hoist features a gearbox, slipping clutch and brake that are not just premium components, but are also maintenance-free for up to ten years. In combination with automatic cut-off by the slipping clutch and automatic braking in the event of a control failure, this means that KUHN employees can depend on the extremely reliable DC-Pro at their workstations. In addition, the chain hoist’s safety-related functions conform at least to Performance Level c and Category 2 as specified in EN ISO 13849-1.
Absolute operating safety combined with high efficiency
The nine ZVKE double-girder overhead travelling cranes with V-type girders offer both maximum operating safety and efficiency. The diaphragm joints of the V-type crane girder design allow light to pass through. Thanks to the reduced amount of material, the innovative crane girder has a lower deadweight, which is beneficial for the building structure. The overhead travelling crane spans range from 10.4 meters to 28.3 meters.
“The first time I saw the crane was at another customer’s facilities, and I have to say I was impressed right away. The crane girder is almost invisible, since it lets so much light through, and that also gives the impression that the crane is very light.” - Stéphane Schissele, KUHN SAS
Given that all the cranes have a load capacity of 20 tonnes, KUHN MGM will be able to transport larger and heavier agricultural machinery for final assembly and to the shipping area in the future as well. At the end of the production line, five cranes assist with the last assembly steps, making it possible to join the pre-assembled and significantly heavier components. Not only the lifting capacity, but above all precise component positioning thanks to variable control are a huge improvement for the working processes.
Another four ZVKE units are in use at the newly built shipping area, where they load packages of finished components and agricultural machinery onto trucks so that they can be shipped from Monswiller to customers all over the world.
The Demag DMR modular rope hoist makes it possible to integrate mechanical and electrical improvements. Frequency-inverter control of the cranes plays an important role when it comes to comfort and convenience and enables operators in the shipping area to pick up and move pallets with agricultural machinery components or even whole agricultural machines with perfect precision. Cranes can start moving and accelerate at variable speeds, so that operators are able to control the long-travel, cross-travel and lifting motions with precision and focus on taking full advantage of the cargo space in the truck.
Safe crane operation
On all nine cranes, the smart SafeControl system monitors and ensures safe operation at all times. The two-stage cut-off prevents the crane and the trolley from colliding with the limit stops. When the first limit switch is reached, the long-travel or cross-travel speed switches to creep speed. As soon as the second limit switch is reached, the long-travel or cross-travel drive is switched off, gently braking the travel motion. Load sway is prevented with a combination of continuously variable control and limit switches, ensuring that loads will not sustain any damage or damage trucks or their surroundings. Crane operators benefit from the electronic assistance, and the crane provides help and protection in the event of unforeseeable situations.
Two of the ZVKE units operate on a crane runway at the new production section. An optical crane anti-collision system is used to prevent collisions: Dual laser sensors redundantly measure the distance between the corresponding cranes on the runway, and if previously defined minimum approach distances are exceeded, the relevant crane is shut down in a safe manner in two stages.In the first stage, the crane can only be moved at slow speed. In the second stage, the crane is safely switched off. This concept of independent safety shutdown with dual-channel hardware corresponds to safety category 3 to EN 13849-1.
Operating statuses always at a glance
With the Demag StatusBoard on the crane girder, operators can always see the weight of the load on the hook. In addition, the StatusBoard displays the current operating statuses of the crane in real time. These include, for example, the load capacity, total load, overload, service information or the activated assistance and convenience features of the SafeControl system – ensuring transparent and, above all, safe control of the crane.
The special features
The modular KBK crane construction kit enables KUHN MGM to implement the workstation crane systems it needs and it can be extended at any time, if necessary. Crane runways, as well as pillar and wall-mounted slewing jib cranes, can transport the relevant components across the entire area. KBK versions made of steel and aluminium are equally suitable for various requirements and can also be combined.
The smooth running characteristics behind the Demag components make fast and safe handling possible while also enabling workers to position individual parts effortlessly and with maximum precision for assembly. Accordingly, the light crane system makes it possible to have effective work processes while maximizing productivity and efficiency.
The V-type girder design with diaphragm joints makes lightweight construction possible, which is beneficial for the building structure. The smart SafeControl system offers maximum safety in crane operation. Long-travel limit switches and an optical crane anti-collision system provide operators with electronic assistance and help to prevent accidental damage in the crane’s operating area. Together with variable control for the long and cross-travel units and lifting motions, this makes crane control much more convenient.
Interview
We interviewed Stéphane Schissele, the building and maintenance manager at KUHN MGM SAS in Monswiller, France.
Demag: Mr. Schissele, could you briefly introduce KUHN MGM SAS and the location in Monswiller?
Stéphane Schissele (KUHN MGM SAS): Monswiller is located in the Bas-Rhin department in Alsace. Our company has deep roots in the region, and we actually have two locations – one in Saverne and another one in Monswiller. The production and assembly plant in Saverne is the KUHN Group’s headquarters.Monswiller is the home of our MGM assembly plant and our spare part production operations. And while on the subject, it’s worth pointing out that “MGM” stands for “Montage Grande Machine”, meaning that this is where our bigger agricultural machinery is assembled. The assembly plant was opened in 2008 with four assembly lines and has had an annual output of 9,000 machines. We’ve now doubled that capacity with the expansion, and right now we have 350 people making agricultural machinery for haymaking, tilling, and sowing. On top of that, MGM specializes in the production of seasonal machinery.
Demag: Why was the investment in the location necessary?
M. Schissele: The first thing was that it was important for us to be able to increase our production capacity from the previous four assembly lines to a total of eight. And to complement that, we were able to add a separate area for logistics and round off the whole production process with a new facility for shipping in Monswiller. In addition to that, one of our defining characteristics is the way we can dynamically adapt to the changing needs of our customers. A few years ago, shop floor widths with working areas of 14 or 15 meters were sufficient for that in Saverne. However, they’ve become inadequate over the years, so we increased that working width to 20 meters at the assembly lines at this location. I can’t overstate how important that is for us, as our machines are becoming increasingly bigger and wider. Long story short, we needed more space for our production operations. Because of this, building the new plant and the recent extension was absolutely vital for us to ensure that we would have the right production environment for our needs in the coming years.
Demag: Can you give us a rough idea of just how big the expansion is?
M. Schissele: The expansion covers about 20,000 square meters that we’re using for productive operations such as assembly, logistics, and shipping.
Demag: What kind of tasks are you using the Demag products for?
M. Schissele: Demag products take care of material handling at the various workstations throughout the plant. The KBK light crane system requires very little effort from our employees when it comes to transferring components to our cathodic electrodeposition shop, as well as for pre-assembly. In addition, most of the chain hoists installed in the KBK systems have a load capacity of 500 to 1,000 kg and are used to handle and position components for assembly. Then, once the sub-assemblies have been put together, we use the hoists to move them to the machine’s main frame. Once there, the partially variable and low speeds of the Demag DC-Pro chain hoists help our employees easily and precisely position the above-mentioned sub-assemblies for assembly operations.
“High-precision installation of sub-assemblies thanks to the variable low speeds of the Demag DC-Pro chain hoists”
At the end of the assembly lines, the machinery undergoes final assembly with the help of V-type cranes which have a load capacity of 20 tonnes.
Demag: What concrete requirements did KUHN have when it came to Demag’s products?
M. Schissele: It was extremely important for the components to have a high degree of operating safety to ensure that our operating personnel would be as safe as possible. Another thing we required was for the products to have a long service life, but we already knew that would be a given based on the many decades we’ve worked with Demag.
Demag: Why did KUHN decide to go with Demag’s workstation solutions?
M. Schissele: We’re still using a very large number of hoists from the PK generation in Saverne today (editor’s note: PK chain hoists were produced from 1961 to 1995), so we’re very aware of just how durable Demag products are. We’ve been using chain hoists from a wide variety of generations on a daily basis for decades now, and they all continue to work perfectly. When our employees let us know that variable lifting speeds would come in handy for their work, we upgrade the hoists with devices from the new DC generation. Also, we’ve tested other products, but the truth is that speeds can be adjusted perfectly on Demag products, which really enables us to get perfect results when installing components. Basically put, higher precision is guaranteed when using Demag hoist units.
“Higher precision is guaranteed when using Demag hoist units.”
Another argument in favour of Demag was the fact that the products can be easily moved by hand. Our hoist units travel almost exclusively on several kilometres of KBK rail. As I mentioned already, the chain hoists have a load capacity of up to 1000 kg, so one might be worried that moving them by hand would be very demanding. But the truth is that with KBK it’s extremely easy! Our employees move loads of up to 1000 kg across spans of up to seven meters without a problem in Saverne and Monswiller. Now, if we instead talk about loads of 2000 kg or more, then it goes without saying that we need electric drives.
“(…) moving loads with KBK is extremely easy!“
Another thing that is indispensable for production planning and flexibility is the ability to modify our workstation layouts. The KBK systems can be modified or extended at any time, and we remove and reinstall some of our cranes at individual production lines 30 or 40 times a year to allow them operate in a different direction, for example. In addition, the KBK system here in Monswiller is set up in such a way as to cover the biggest area possible. All in all, however, it’s impossible for us to determine in advance whether an assembly line will stay the same for eight or ten days, for instance. In fact, requirements can even change daily. 20 years ago, we assembled 1,000 machines on a single line, and now it’s 80, 60, 50, sometimes even only 40 machines. Batch sizes are becoming smaller and smaller, and that means that we need our lines to be extremely flexible. That obviously goes for the crane runways as well.
The solution that we’ve had with KBK for over two decades is, to put it simply, the best solution for us. We come close to the line with the various parts, and our employees can easily move the components to the corresponding workstation for assembly. This happens from workstation to workstation and along the 100-meter-long production lines until we can test the finished agricultural machine at the end of the corresponding line and prepare it for shipping. That’s where Demag V-type cranes come in to help with final assembly and handling the finished products.
Demag: How do you like the V-type girder design?
M. Schissele: That’s really something new. We’ve been using KBK equipment for years, but the V-type girder for the cranes is quite the innovation. The first time I saw the crane was at another customer’s facilities, and I have to say I was impressed right away. The crane girder is almost invisible, since it lets so much light through, and that also gives the impression that the crane is very light.
Needless to say, the lightweight design is also good for the facility’s steel superstructure, and that’s before you even consider the fact that the design is aesthetically perfect. Add the technical specifications, available load capacity despite the low deadweight, and speed to that and what you get is a solution that’s really something. Moreover, the whole thing is reflected in the lower wear experienced by the travel wheels and the runways, which results in lower costs for us. It’s also worth mentioning that we actually ran the numbers for systems offered by the competition, and what we found out was that the conventional crane sections in them were heavier and taller, which would have resulted in a much taller crane runway. We’re talking a difference of up to one meter here. That simply didn’t work for us, so we decided on the innovative design instead.
“The V-type crane is a really excellent product. That’s why we decided to go for the new design immediately, and let me tell you, it outdid our expectations.”
We expect the cranes to keep delivering good results for a long time, and in fact oversspecified them a bit with their load capacity of 20 tonnes. But like I already mentioned, our machines are getting bigger and bigger and heavier and heavier, and a reserve load capacity of 5 tonnes really didn’t make any difference in terms of price.
Demag: How do you make sure that the systems are available at all times?
M. Schissele: The simplified spare parts management approach is a huge advantage. We order a large number of spare parts directly through Demag Shop.That’s a fast and efficient system in that we can also look at the number of KBK suspensions and have drawings be generated. I can’t overemphasize how useful that is. And after the simulation, I can simply order the products directly. It’s something we do very often, and the process of getting information, selecting parts, and getting things delivered is always extremely fast. Now, before that, I used to find the best products with the catalogue, and that was already pretty effective and fast, but Demag Shop has made things even easier.
We have a store with Demag products at both production locations, so we have a central source of spare parts. We have products spanning more than 25 years stored there, and nearly all of them are compatible with each other, which of course is extremely advantageous and helps us maintain the degree of flexibility we need.
Demag: Did you also use Demag Shop to plan the production expansion?
M. Schissele: We mostly use it to configure smaller projects, of say up to about three cranes. That works perfectly! But when it’s a big, full project, it’s always better to have someone who can assist us and help us plan the whole process. In this case, that was the Demag sales team, and they were extremely effective. The parts arrived sector by sector. The parts were pre-sorted in such a way that all the KBK components and hoist units required for each sector came together. Needless to say, we discussed delivery times in advance, and the corresponding packages arrived at our work site at the scheduled times. That means that we didn’t have to store a lot of stuff at the site and that our employees were able to install and assemble the systems right after delivery.
“We’re 100% satisfied with our Demag solutions.”
Demag: When you look at the Demag solutions you’re using, what would you say are the biggest advantages they offer?
M. Schissele: Demag products provide enormous flexibility and make it possible to manufacture complex assemblies in small areas. The products have extremely long service lives.They can also withstand some serious loads, and have individual components that can be ordered even after 20 or 30 years without a problem. In addition to that, our need for optimal operating safety is something that Demag products meet to a T. We’re 100% satisfied with our solutions.
Demag: What kind of impression do your employees have when it comes to working with Demag products?
M. Schissele: Our employees are very happy! They can move components quickly. However, there’s an even bigger advantage, and that’s the fact that they can efficiently position parts for putting together sub-assemblies with absolute precision. And that’s not just with the light crane system at the workstations, but also with the cranes at the end of the assembly lines and in our shipping operation.
Image gallery
Image gallery
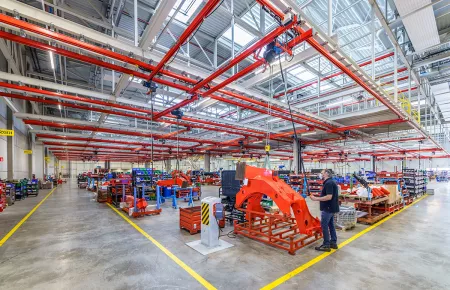
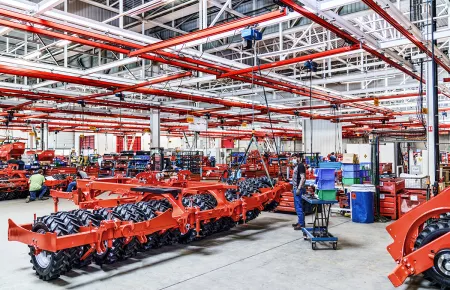
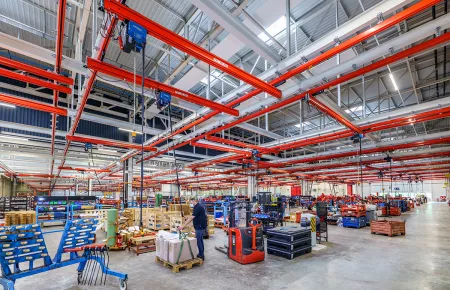
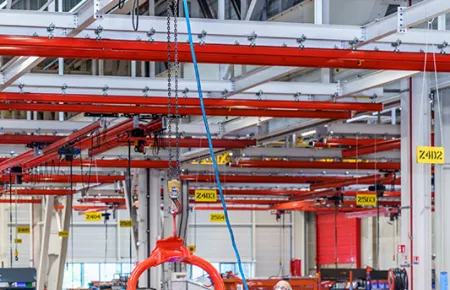